Powder Coating
Powder Coating is a technique to color material that involves free-flowing dry powder ionized to cling to the work surface.
Custom Sign Powder Coating
Powder Coating does not require a solvent like liquid paint. The powder is applied with an electrostatic charge and then baked to create a skin to the material, which is more durable and weatherproof than standard paint.
The powder is typically applied using a specialty sprayer that charges the powder particles so that they are attracted to the grounded workpiece, which must be conductive to be correctly painted, like our hand-made metal signs.
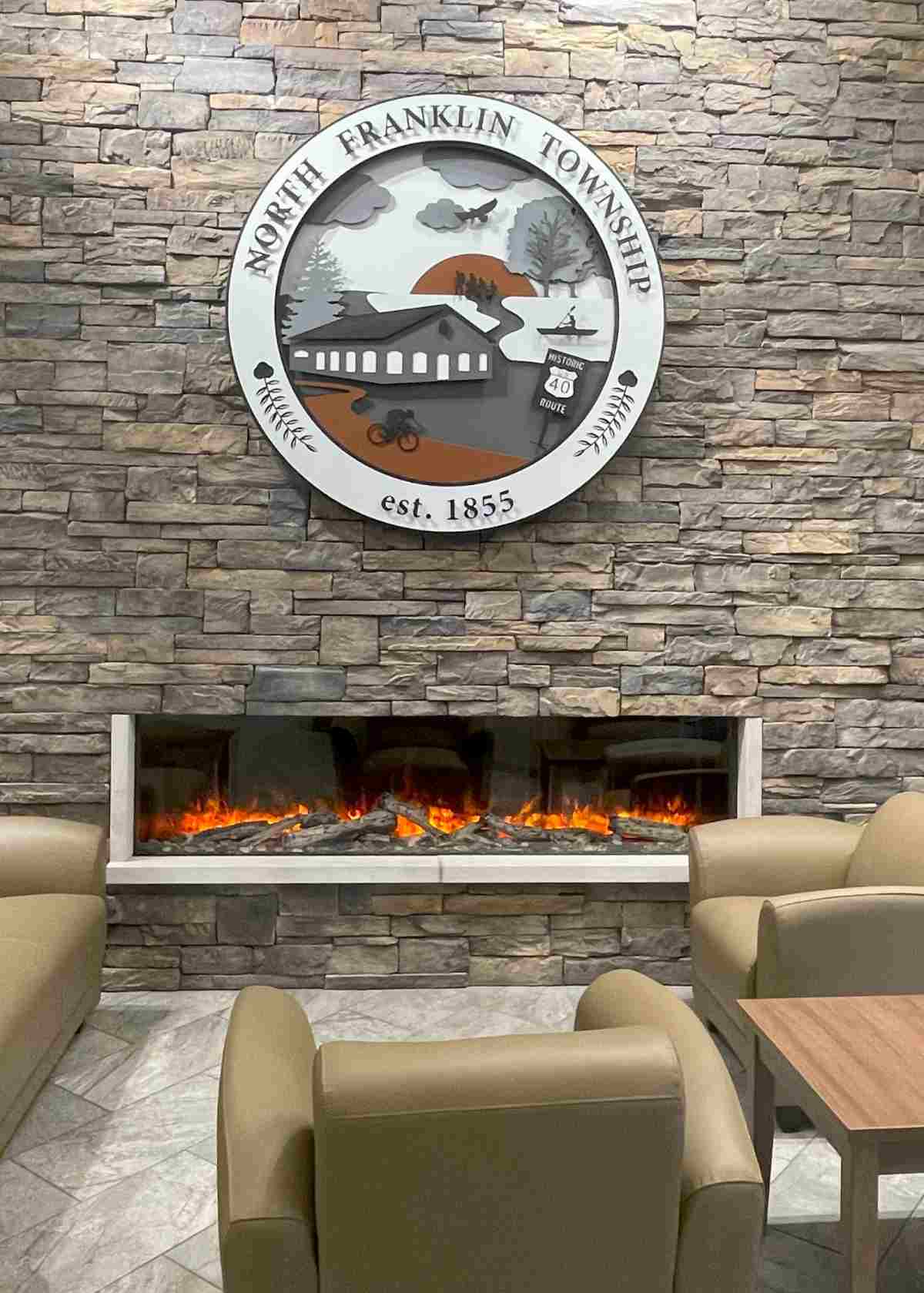
Featured In
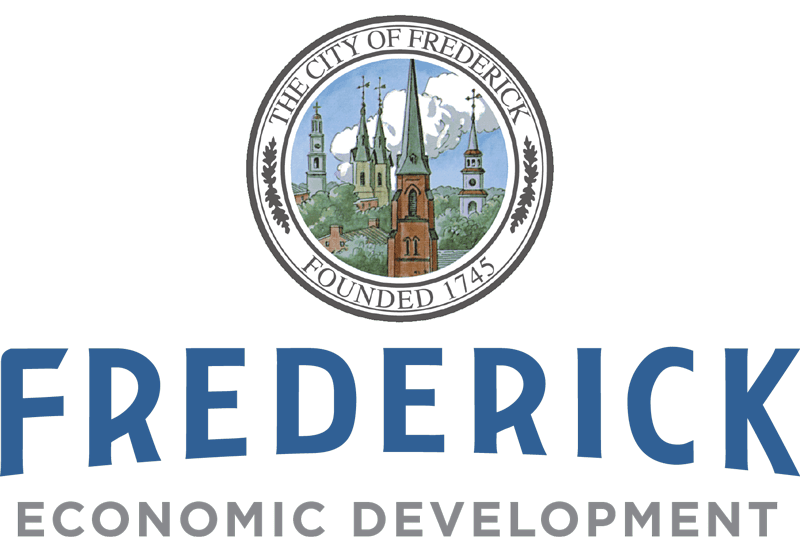



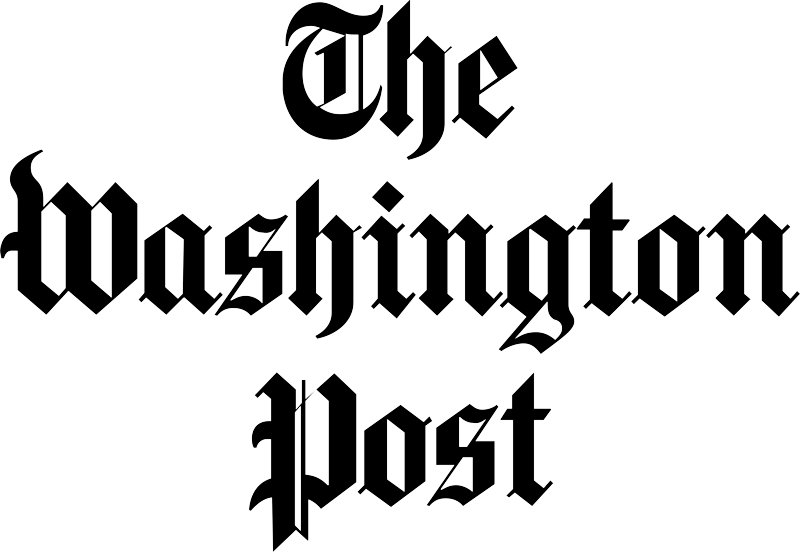
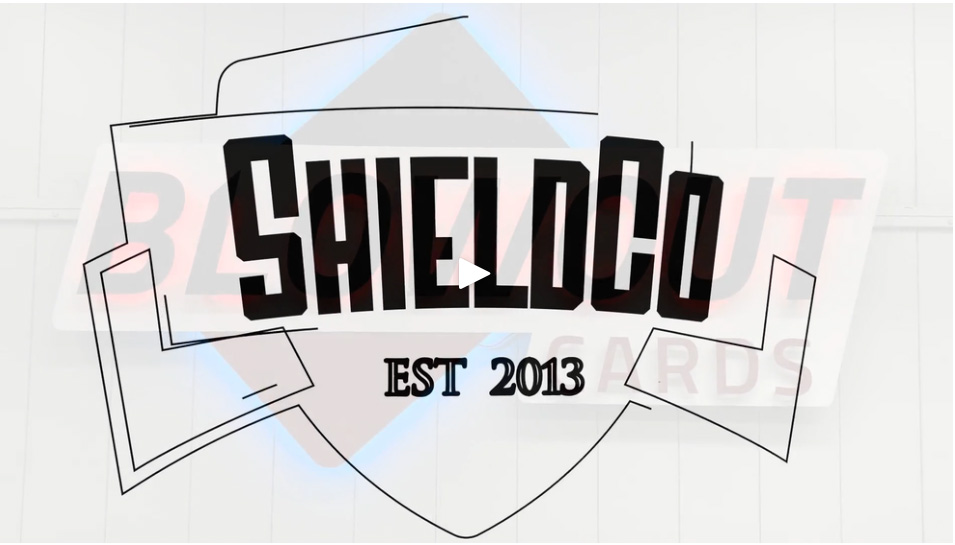
Why Powder Coat Your Sign?
There are multiple advantages to using powder coats over regular paints when coloring your product:
Safer Process
Powder coatings emit little to no VOCs, eliminating the need for costly pollution controls.
Consistent Application
Powder coatings provide thick, even coverage without runs or inconsistencies.
Chipping Resistant
Thermal bonding makes powder coats highly resistant to chips and scratches.
Professional Appearance
Powder coating delivers a smooth, uniform finish for a high-quality look.
High-Quality Finishes
Powder coats offer versatile effects and finishes that are impossible with other methods.
Faster Curing Time
Powder coating cures much faster than liquid paint applications.
Custom Powder Coating for Your Sign
We take pride in our custom sign fabrication services to bring you the most visually impactful product on the market.
FAQs
Powder coating provides a durable, smooth, and vibrant finish that protects the metal from rust, scratches, and wear. It enhances color, texture, and longevity, ensuring your artwork stays beautiful for years to come.
The cost of powder coating depends on the size, complexity, and color of the piece. Typically, prices range from $50 to $300 for smaller projects, while larger or more intricate pieces may cost more. Contact us for a custom quote.
Powder coating is highly durable and can last for decades. Its resistance to rust, chipping, and fading makes it ideal for both indoor and outdoor use.
Ready To Learn More? Reach Out Below!
We’re here to bring your ideas to life with expert craftsmanship and tailored sign services. Reach out now to discuss your custom sign.
Step 1
Fill out our form with details of your project.
Step 2
We follow up to ensure we understand your vision for the sign and where we share some ballpark pricing to help decide the best sign style.
(For those with smaller project needs, please note we typically have a project minimum of $1500.)
Step 3
We get to work on your quote and a 3D mockup to show you how it will look in real life.
Get A Free Quote
Ready to bring your brand to life with a custom sign? Get your free quote today!
Book A Meeting
Want to speak with ShieldCo team about your vision? Book your meeting now.
Customer Reviews
See what our customers are saying.